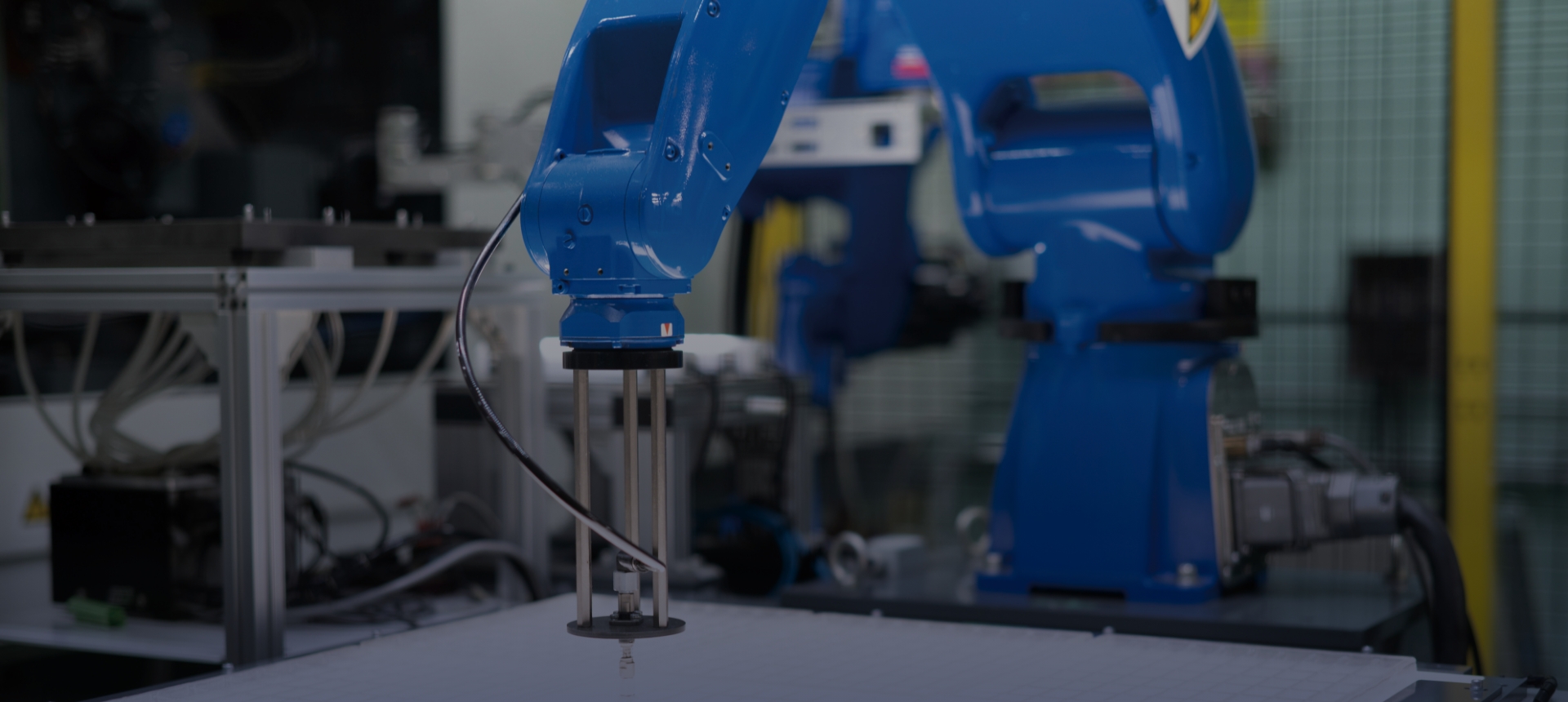
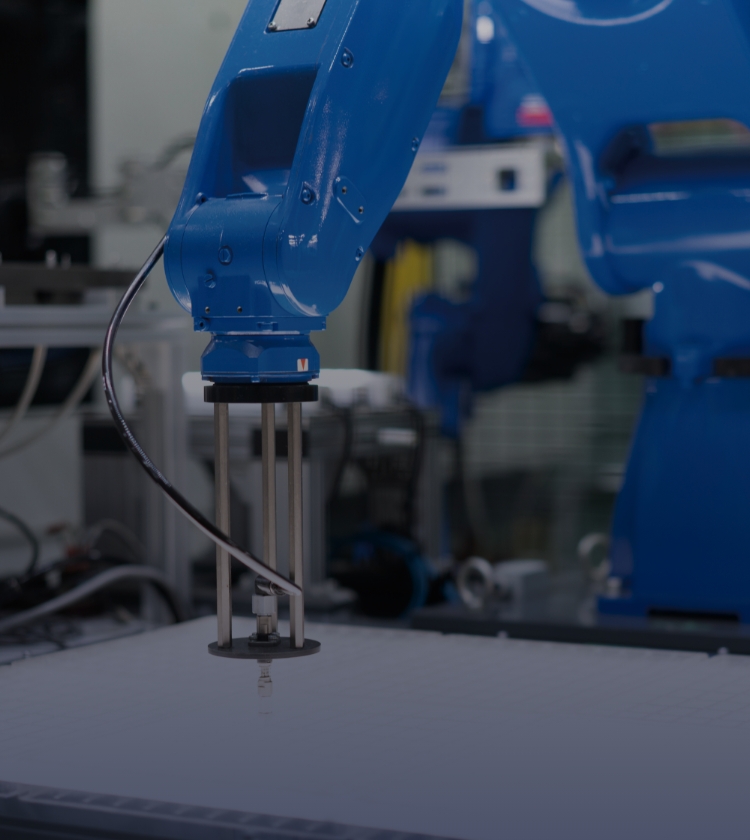
諦めない精神で
ロボット化を実現!
精密な超高精度工業用部品のインサート成形
Project #02
貴社でこんな部品を作るのは難しいですよね?
精密な超高精度工業用部品を作る依頼だった。
三優ライト工業では数々の特殊なインサート成形品を製造してきた。
だが、今回の依頼はこれまでに以上に精密で
その品質を維持したまま量産をする必要があった。
プロジェクトは試行錯誤の繰り返し。
だが、技術に限界はない。
絶対に諦めない精神と
情熱を絶やさず挑み続けた
ひとつのプロジェクトストーリー。
-
代表取締役
T.M
-
製造部 金型課
T.I
-
製造部 成形課
Y.M
-
製造部 成形課
T.I
Chapter 1
当時、産業用ロボットを使った超高精度工業用部品のインサート成形は三優ライト工業で初めての試み。立ち上げに際しての最重要ポイントは「いかにお客様の図面仕様通りに品質を維持しながら連続生産出来るか」だった。
依頼のあった超高精度工業用部品はこれまで以上に高い精度が求められ、汎用的な産業用ロボットでは対応することができなかった。いきなり大きな壁がプロジェクトチームに立ちはだかる。
ロボットを使った
インサート成形の実現に向けて
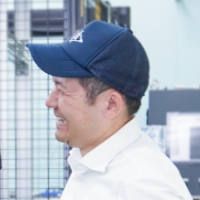
この製品は、金属板と樹脂を一体化させてはいるが、板厚が0.8mmしかなく、更に製品形状になった場合、0.4mmしか飛び出していません。
要するに金属板は0.4mmしか金型に潜っていないという事になります。
人間の手作業では微調整も出来るが、汎用の産業用ロボットにその精度が出せるかどうか。また、ロボットは精度が出ても、操るのは人なので、安定的にティーチング含めて実現出来るのか。という事が最大のポイントでした。
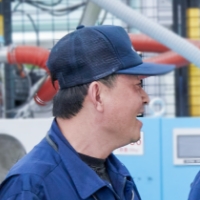
これまでも他の製品で使われていた産業用ロボットがありましたが、客先から支給される金属板は、バラバラに色々な方向に向いていたり、金属板の金型への潜り込み量が0.4mmしかない為、ロボットには非常なる精度が要求されました。
もしも金型への挿入でズレが発生した場合、即金型事故が発生します。色々な方向に向いた板をピッキングして、それを高精度で金型に入れて行く、金属板は6枚もあるのに不可能に近い状況でした。
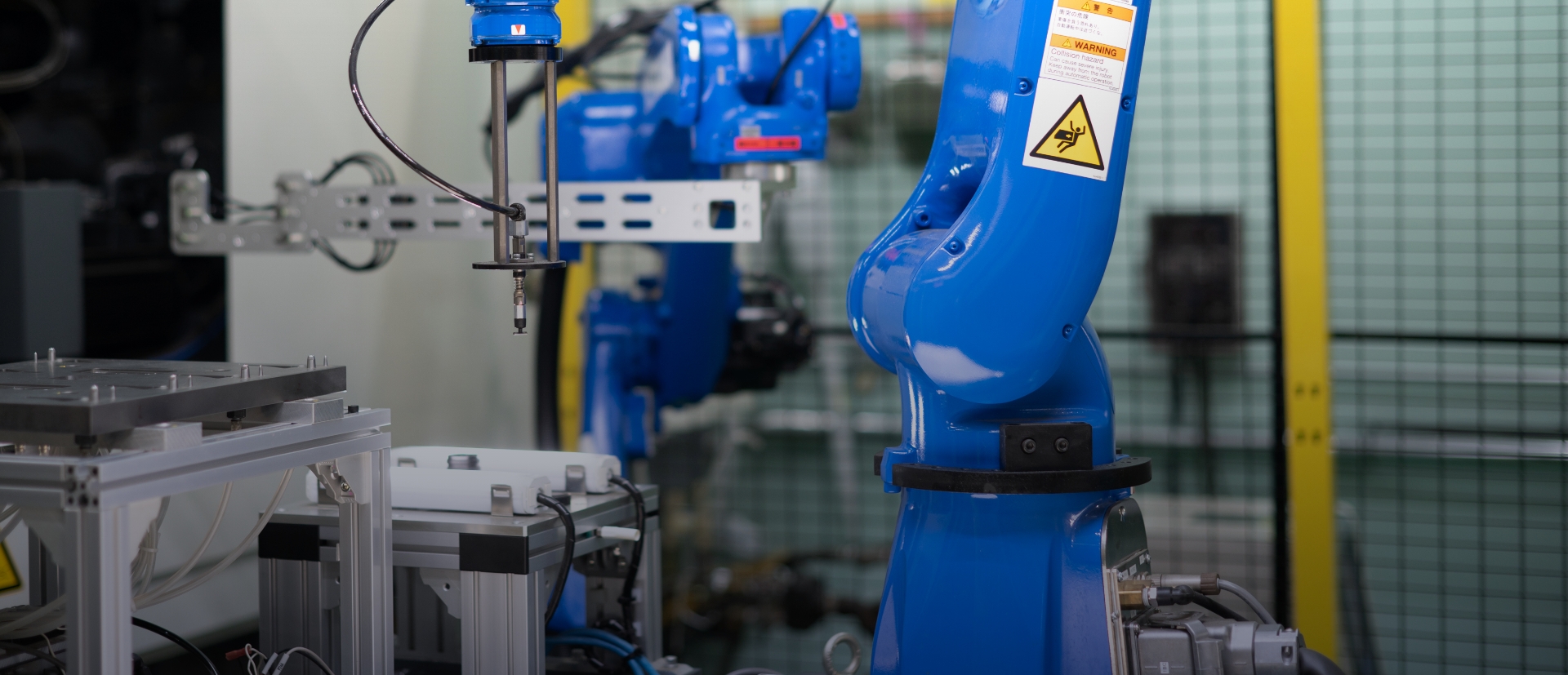
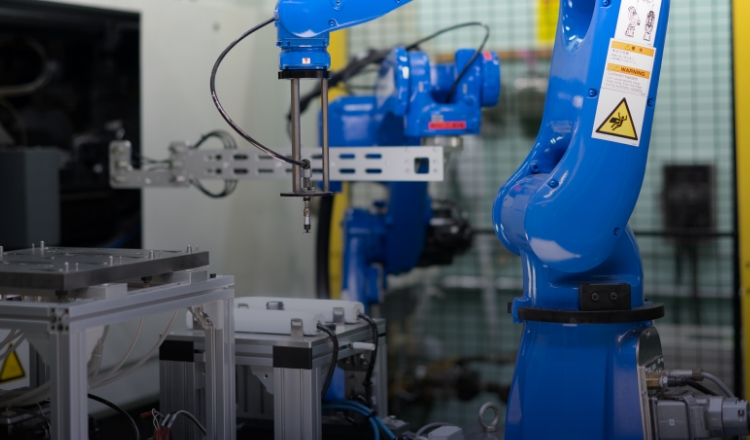
Chapter 2
難しい課題に直面したチームが出した答えはリスクを恐れず挑み続けるということだった。これまでの方法とはまったく違うアイデアが問題解決の突破口を開く。
2台のロボットを
組み合わせるアイデア
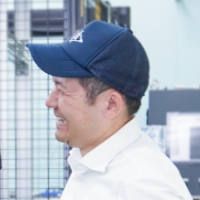
最初は機械を一台だけ動かし、二種類のパーツができるように考えていました。
ただ、その方法だと、人がずっとつきっきりになるため、人の手を必要としない自動化を目指そうということになりました。
そこで、ロボットに役割を持たせて、1つの仕事を1つのロボットで役割分担する事で解決できないかという案が出てきました。
1台はピッキングロボット。このロボットは、お客様から届く色々な方向に向いた金属板を徹底的に高精度で位置を決めステージに搬送する。
もう1台はインサートロボット。このロボットは、1台目が高精度で位置を出してくれた金属板を掴んで、高精度で金型に挿入する役割を持ちます。
メーカーではなく、我々のような成型屋さんで、ロボットを開発して自動化を行っているのは少数だと思います。
ロボットを作ってくれる会社にも何度も足を運び、デモ用に金型を何度も作ったり、きちんと挿入ができるかなど何度も試したり。
なかなかその精度に満足するというのは難しいなと…。
途中、本当にできるのか?と疑問が湧いたりもしましたが、いやいやきっとできると言いながら。
最初はずっと警告音がピーピーなっていて…。
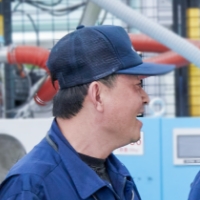
最初はずっとなってましたね。
成形機の検知機構でインサートの位置がズレるとエラーになります。
エラーに加えてプレッシャーや不安もたくさんありました。ロボットメーカーにもこのような実績はなかったですし、我々も初の試みでした。
金型を作ってはロボットメーカーに持っていき、いろんな想定を考えながら、こうしたときはどうする、入らなかったときはどうするって。理論ではなく予知するしかない。進めながら改善していく感じでした。
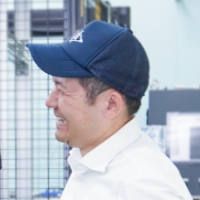
ずっと警告音がなっていたんですが、調整を繰り返すことにより、自動で成形できるようになっていき、一人がずっとつきっきりの状態はなくなっていきました。
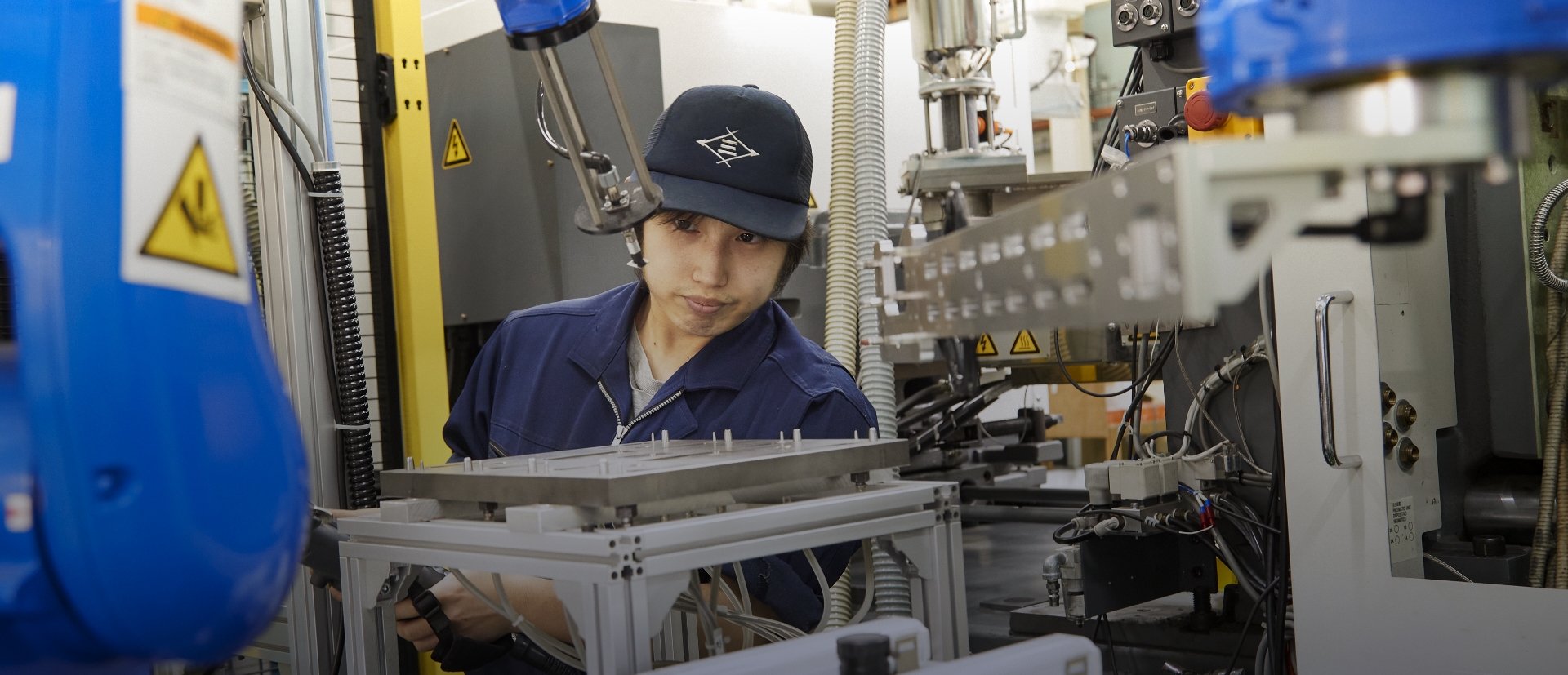
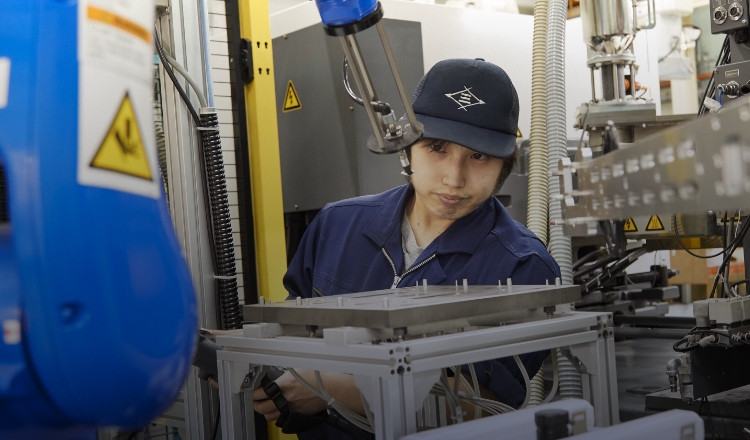
Chapter 3
試行錯誤を経て、いよいよ立ち上げの段階までは到達した。ここから量産体制に向けて別のメンバーにバトンが受け継がれるが、それもまた簡単な道のりではなかった。
しかし、情熱を絶やさない若いメンバーを中心に、プロジェクトはゴールへと進んでいく。
量産に向けてのバトンタッチ、
続く試行錯誤
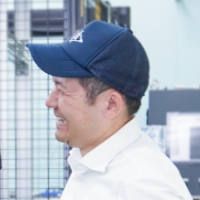
受注をいただいてから、ここまで試行錯誤をして大変でしたけれど、ある程度の波が作れてからは若いメンバーにバトンタッチをしました。
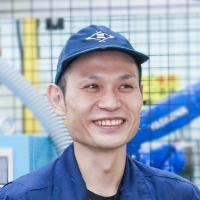
立ち上げ時にもありましたが、インサートを金型に入れるときに、うまくいくようになったとはいえ、それでもズレてしまうことがあります。
1時間に1回とかのレベルなんですが、量産するにはこれでは多すぎで、その原因をさぐるのが一番大変でした。
最初は供給する台が悪いのかと思い、汚れを拭いたりあらゆる可能性を潰していくんですが、それでもまだアラートが鳴ってうまく行かない。
次に、取り出し側の吸盤がわるいのでは無いかと考え、吸盤のパーツをローテーションして試したり、新しいものに取り替えたり、そういった原因の可能性をどんどん探っていって対策を進めていくにつれ、どんどんトラブルを減らしていくことができました。
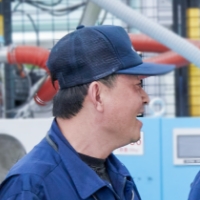
量産フェーズでのトラブルは立ち上げ段階でも予想できていた部分もありましたが、消耗品であったり、機械の力加減によって、それが量産に実際入ってみないと、どれぐらいの頻度で起こってくるかは運用しながら改良していく必要がありました。
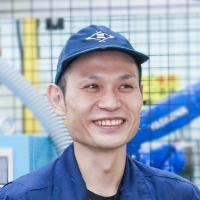
何時何分にアラームがなったかなど一個一個メモを取りながら、機械のパーツの材質を変えてみたり、メーカーを変えてみたり。
もちろん今もなお、全ての問題がなくなったわけではありませんが、少しでも精度を上げることができるようにと、日々現場で改善を続けています。
あと、現場ではトラブルのあったときどのように対策したかというのを必ず書くようにしています。自分自身、同じトラブルがあったときはもちろんのこと、違うメンバーがそのトラブルに遭遇したときに、同じようにリカバリができるように、みんなが現場で困らないような工夫も重ねています。
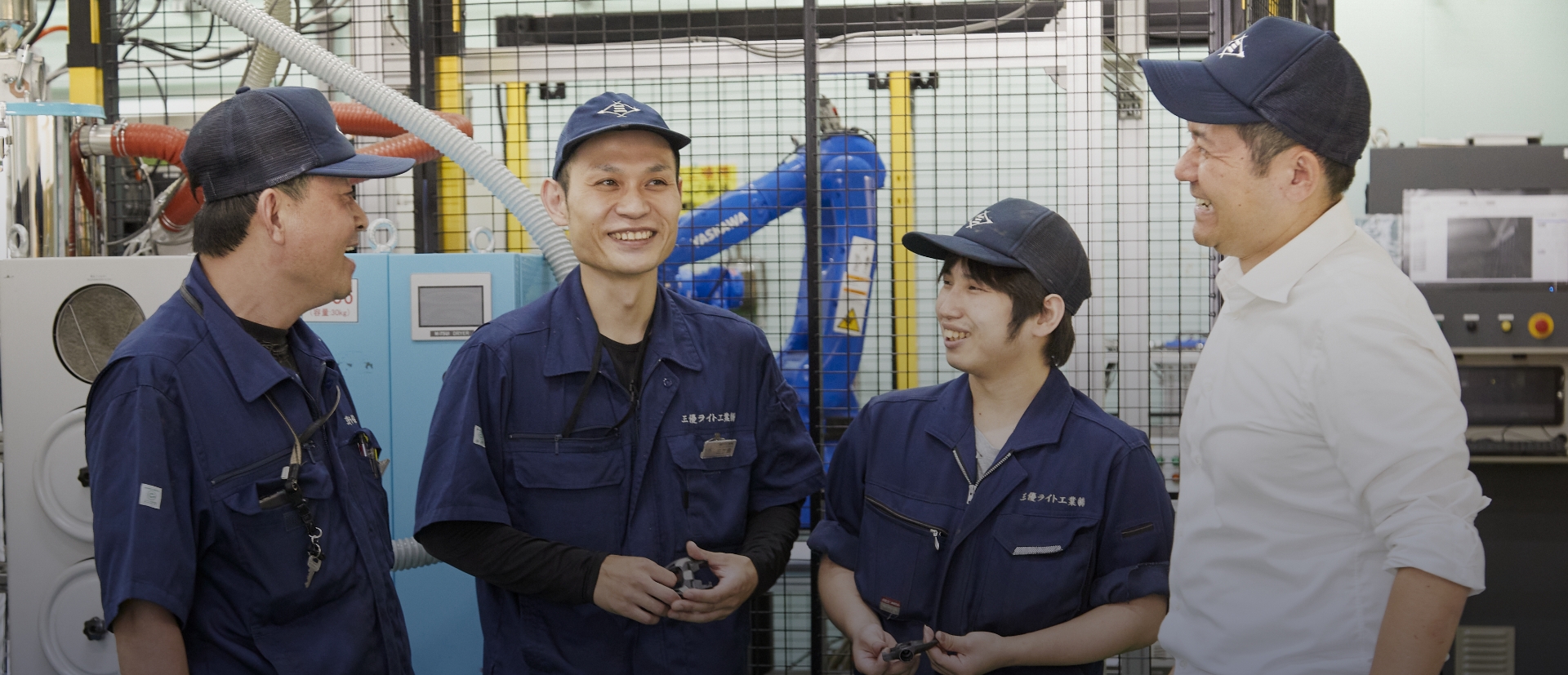
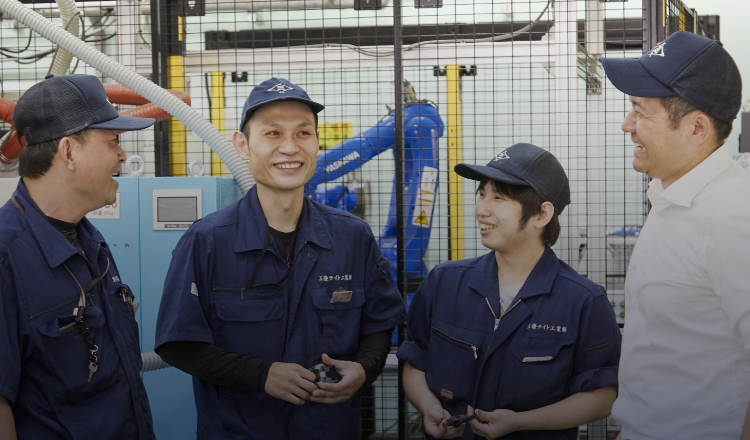
Chapter 4
挑戦を学びや気付きに変え、プロジェクトを重ねるごとにチームは進化していく。それが困難であればあるほど、さらにその成長はさらに加速していく。絶対諦めない精神と、より良いものを作りたいという現場の熱意が、ひとつひとつの壁を乗り越えていく原動力となる。
まだまだたくさんやれることがある!
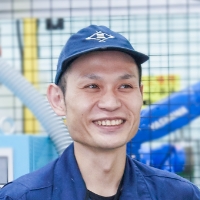
このプロジェクトで発生したトラブルは、他のプロジェクトでも起こり得ることが多いと考えています。今後も応用できる、社内の共有知識が増えたことが大きいと感じています。
私は産業用ロボットをこれまで扱ったことがなかったので、それを操作できるようになったのも今後の自信に繋がっています。
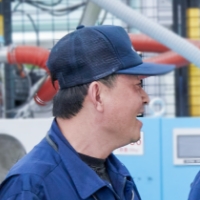
今回のプロジェクトを経て、我々はいろんな可能性を感じることができました。
ロボットをこういう使い方もできる、こういうものも作れるんだと。
スタートから様々な試行錯誤をして、いろんな経験をすることができました。
今後どんどん求められていくことが増えていくと思っていますが、ロボットの導入がなければ難しくなっていくはず。今後仕事をしていく上でも、会社としても自分自身も勉強となりました。
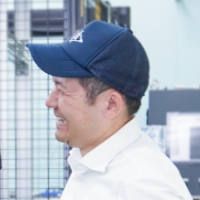
このプロジェクトがあって本当に良かったと今思っています。立ち上げから量産開始まで、すでに何年か経っていますが、今も順調に生産を続けることができています。
実際にロボットを導入して成果も出ましたし、客先からのクレームもありません。そして何よりも若いメンバーが率先してプロジェクトを引っ張っていってくれていることが会社にとっても嬉しい事でした。
彼らが活躍してくれているというのは、非常に楽しみですし、ますます会社としてもできることの幅が広がっていくと感じています。
みんなで諦めずにやってきたことが、少しずつではあるが成果として出ていることが素晴らしい。
まだまだたくさんやれることがある。今後のプロジェクトにも活かしていきたいと思います。